Environmental Management System
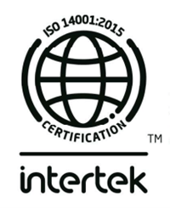
The natural beauty of the Midwest is as striking today as it was over 110 years ago when Northern Engraving was founded. We treasure this natural environment and promote conservation, recycling and efficient use of energy throughout our facilities to minimize the impact on the environment and to reduce operating costs.
Northern Engraving operates two main manufacturing campuses in Sparta and West Salem, Wisconsin and a satellite facility in Spring Grove, Minnesota. All of which are registered to the international environmental standard, ISO 14001:2015. Our management system is based on areas of focus including environmental, quality and safety. This includes processes to identify and adhere to customer specific environmental requirements such as IMDS reporting and RoHS compliance.
Northern Engraving is committed to continual environmental improvement. Central to this commitment is maintaining a robust environmental management system following the ISO 14001 standard. This system gives our manufacturing sites the tools needed to analyze environmental impacts, set objectives and targets, develop supporting programs, review results and redirect efforts. Employee involvement at all levels is a key component in the ongoing success experienced by each facility.
Corporate registration is maintained through successful annual audits from the third-party registrar Intertek.
Environmental Certification
ISO 14001 Certification
Environmental Policy Key Points
- Continual Improvement
- Meet Environmental Obligations
- Reduce Waste
Environmental Objectives and Targets CY 2025
-
- Sparta, WI Campus:
- Objective: Reduce facility hazardous waste generation by 2%.
-
Target: Establish distillation of solvents by 10-1-2025.
- West Salem, WI Campus
- Objective: Reduce facility energy consumption by 2%.
- Target: Establish energy baseline of the LCS department by 7-1-2025.
- Sparta, WI Campus: